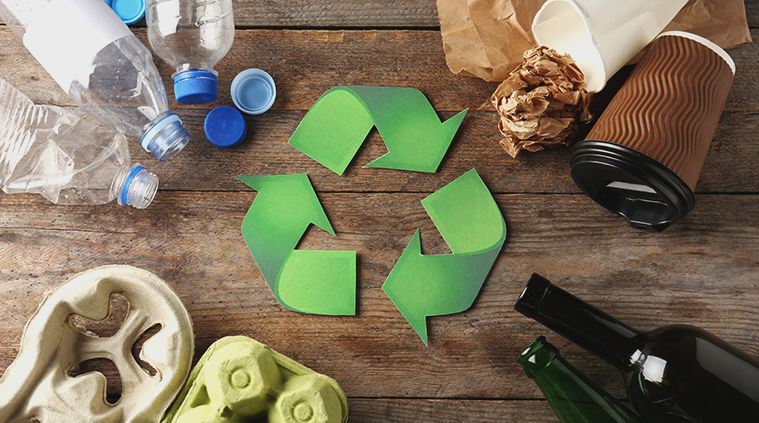
Optimized Materials and Processes Make the Difference
Sustainability isn’t just a trendy word. It can make a measurable difference in the efficiency and profitability of your business—while also making you a better citizen of the planet. Here are five steps you can take right now for a more sustainable future.
Sustainability has become little more than a buzzword for too many consumers and businesses. That’s unfortunate. The long-term health and quality of life on earth depends on a rapid turn to more sustainable practices in the manufacturing, transportation and consumption of goods.
Most businesses don’t consider long-term, global issues when they’re focused on quarterly results. However, there are also self-serving, shareholder-pleasing reasons for putting sustainable packaging designs into place right now—even while knowing that the fight for our planet’s future calls for continual vigilance and adaptation.
True sustainability in the choice and use of industrial packaging supplies can reduce your raw material costs, scrap and waste-handling burdens. It can reduce your regulatory compliance costs and risks. It can strengthen your brand by demonstrating your care and commitment for the well being of employees, customers, the local community and the world. The eco-friendly packaging solutions you put into place right now will set you up for lasting business success.
Here are five simple ways you can become more sustainable—and potentially more profitable—beginning right now.

1. Optimize Usage of Packing Materials
Virtually every consumer who has ordered goods online has felt guilt over the amount of waste in secondary packaging materials required for shipping. Multiply that guilt many times over for businesses that order items by the pallet, dealing with far greater volumes of secondary packaging as well as tertiary packaging. Excess packaging is also major cost driver in addition to the environmental impacts.
Proper automation can all but eliminate waste of corrugated fiberboard, void-fill materials, films, adhesives and more. Automation enables consistent application of the minimum amount of material that can provide eco-friendly product fulfillment while ensuring reliable protection—from the manufacturing facility to the warehouse, from shipment to final destination.
For example, one of our customers used automation to reduce stretch film consumption from 1 million pounds to 800,000 pounds—a savings of 20% with no compromise to product protection.

2. Optimize Shipping Sizes
We’ve all wondered why a small product—a package of batteries, for example—comes shipped in a relatively large box with excessive void material to keep the product from rattling around. It’s an unnecessary waste, and the same problem occurs at larger scales, all the way up to entire pallets and shipping containers filled with vastly more packaging than the actual products.
By optimizing shipping sizes, you can minimize the amount of packaging and void-fill material needed, greatly reducing material costs and waste. You can enable shippers to transport products with much greater efficiency, helping to minimize greenhouse gases and highway wear and tear. Plus, optimized sizing can minimize DIM weight (dimensional weight) charges and help ensure you’re paying the lowest rate with each shipment.
3. Improve Void Fill By Using Eco-Friendly Packaging Materials
Void fill has always been a big problem for sustainability. Polystyrene peanuts and bubble wrap contain little or no recycled content, are bulky and expensive to ship, and are almost impossible to recycle. Inflatable packing pillows tend to be one-size-fits-all, often leading to underprotection of the product or oversizing of the box. Virgin paper production depletes wood resources, alters natural ecosystems and decreases the carbon-storage capacity of forests.
Plastic and paper void fill materials won’t be going away anytime soon, but smart packaging can minimize their environmental impacts. For products that aren’t fragile, heavy or subject to damage, a well-fitting box with no void fill may be all that’s required. Inflatable pillows can be size-optimized to decrease the amount of material required, the box size and the shipping weight without compromising product protection. And 100% post-consumer, recyclable and compostable packaging can replace virgin paper and non-recyclable materials.
As an example of the latter, Amazon’s familiar white bubble mailers have never been curbside-recyclable. They either get thrown out by the consumer or improperly placed in the recycling bin only to be laboriously removed from the recycling stream. But as consumers have demanded greater sustainability, Amazon has responded by introducing an innovative padded mailer made of paper that can be recycled in the same curbside bin as the company’s shipping boxes.

4. Control Human Factors That Lead to Waste, Product Loss and Excess Costs
Industrial automation on the packaging line ensures consistent use of materials from pallet 1 to pallet 500, significantly reducing material waste that can be caused by human variability and error. Automated consistency also helps minimize damage due to improperly packaged and wrapped products. Automation reduces not only the expense of material waste and product loss, but labor costs as well.
For example, one of our customers had been using a stretch wrapper that required manual settings. The forklift driver had to exit the forklift to wrap each individual pallet. Ensuring a consistent wrap is beyond human capabilities. Material was inevitably wasted and products damaged in the effort to achieve a secure wrap every time. The constant need to move from forklift to wrapping machine and back to forklift was labor intensive, time consuming, and an unnecessary safety risk.
We designed a process that only requires the forklift driver to drop pallets in front of a machine that auto-wraps each pallet with the optimum amount of material—saving time and money while ensuring consistency, reducing material waste and product loss, and improving safety.
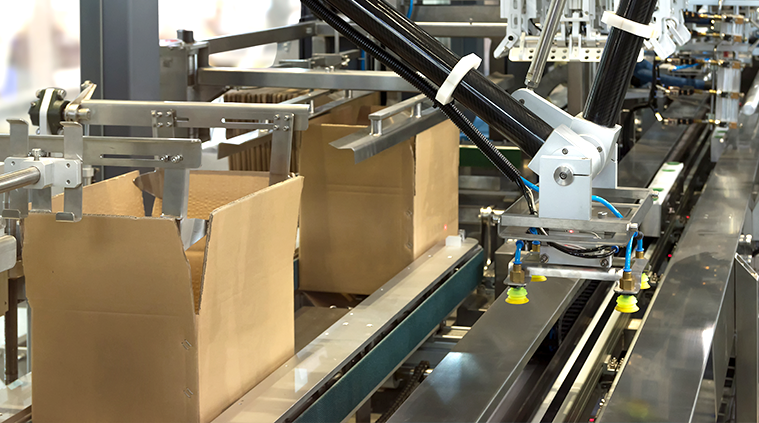
5. Reduce Overall Energy Consumption Through More Efficient Lines
Sustainable packaging solutions reduce your reliance on forklifts, fossil fuels, resource-intensive materials, costly machinery and inefficient processes. Clean, optimized automation lines consume less energy, saving money and reducing your company’s carbon footprint.
At North American, sustainable processes are a specialty. We have a unique ability to rapidly evaluate your current processes, design options for more efficient and sustainable industrial packaging based on your actual operating environment, model the results, and calculate the savings to your material usage, energy consumption, labor costs and bottom line.
Interested in a more sustainable future for your business? Contact us to learn more or to schedule an evaluation. We understand your sustainability aspirations. Let’s achieve them together.